Materials
Help, guidance and technical support
Your contacts for industrial fastening systems
EJOT’s advanced fastening systems are found in countless industrial and engineering assemblies around the world. Click below for sales and technical support from one of our experienced team. We conduct inspections and observations onsite, in addition to providing help and advice direct from our UK manufacturing centre.
We manufacture metallic fastening element from the following materials:
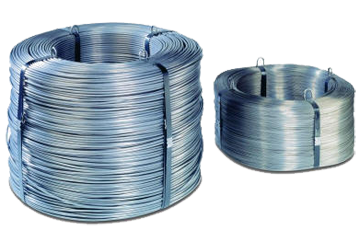
- Low Alloy Steel - acc. to DIN EN 10263-2 (for fastening element without heat treatment, e.g. C10C)
- Case Hardened Steel - e.g. SAE 1018, SAE 1022
- Through Hardened Steel - e.g. SAE 1022, 23MnB4, through hardened to e.g. Rm min. 1040 N/mm² Standard for EJOT PT® , DELTA PT® , Duro-PT® , ALtracs® Plus
- Austenitic Stainless Steel A2 1.4303 - X4CrNi 18-12 (preferred material for self-tapping screws Ø >= 3.0 mm)
- Austenitic A2 Stainless Steel 1.4301 - X5CrNi 18-8
- Austenitic A2 Stainless Steel 1.4567 - X3CrNiCu 18-9-4 (preferred material for micro screws Ø <= 2.5 mm)
- Austenitic A4 Stainless Steel 1.4401 - X5CrNiMo 17-12-2 (upon request)
- Ferritic Stainless Steel F1 1.4016 - X6Cr17 ferritic chrome steel
- Aluminium Materials – Upon Request
For orders of screws made of stainless steel, please note:
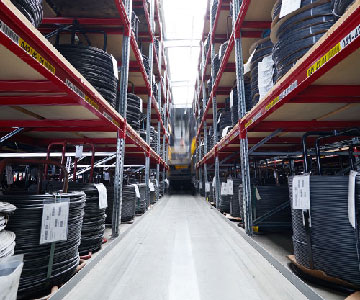
The term " stainless steel" describes a group of steels with a surface coating with a high oxide content. Part of this, is the group of austenitic stainless steel (A2 and A4 stainless steel). This oxide coating is also called passivation layer and is needed for the corrosion protection. Even in case of damage this passive coating continuously re-appears under the influence of oxygen. The formation of the passive coating can also be accelerated by additional chemical passivation (e.g., acc. to ISO 16048). This passivation cannot be compared to an artificial passivation on zinc. Unless otherwise agreed, the fastening elements have to be delivered clean and bare base metal acc. to DIN EN ISO 3506-4. In order to reach the best possible corrosion resistance, we recommend passivating. If passivating is requested, it has to be done acc. to ISO 16048. The corrosion resistance of austenitic stainless steel cannot be determined with a salt spray test. The salt spray test is designed as a test method to show weak spots in coatings (e.g. galvanic coatings or organic / inorganic coatings). Fasteners made of austenitic stainless steel that are salt spray testes, will definitely rust. The reason is that the oxide coating is destroyed by the salt spray and no new oxide coating can form due to the permanent spraying. For this reason, the corrosion protection of stainless steel screws cannot be compared through a salt spray test with galvanic or inorganic/ organic coated screws. We are not aware of any standards where stainless steel fasteners are put through a salt spray test. If a fastening element made of austenitic stainless steel is exposed to oxygen and thus forms an oxide film, this fastener will always show a better corrosion protection than a common fastener made of low-alloy steel (with a galvanic or inorganic / organic coating)